Dashboard moulds are essential tools in the plastic injection molding process, primarily used for manufacturing various dashboard components in automobiles and other applications. These molds are designed to create intricate shapes and features that are not only aesthetically pleasing but also functional and durable. Understanding the nuances of dashboard moulds can greatly enhance the efficiency and quality of production processes in the manufacturing sector.
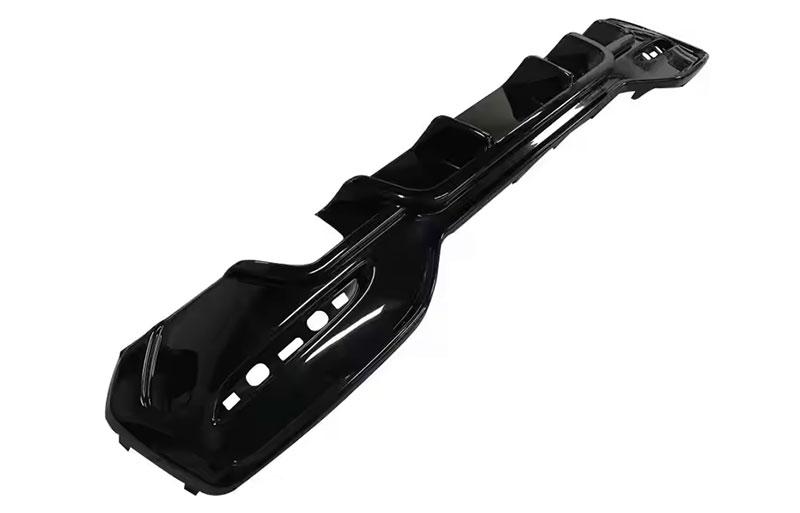
The primary function of a dashboard mould is to shape molten plastic into a desired form. This is achieved through a process called injection molding, where plastic pellets are heated until they become molten and then injected into the mold cavity. Once the plastic cools and solidifies, the mould is opened, and the finished part, which can include features like vents, gauges, and control panels, is ejected. The precision in crafting these molds is crucial, as even the slightest deviation can result in defects or misalignments in the final product.
When designing a dashboard mould, several factors must be considered. These include the type of plastic being used, the complexity of the part geometry, and the expected production volume. High-quality molds are typically made from durable materials, such as steel or aluminum, which can withstand the high pressures and temperatures involved in the injection molding process. Additionally, features like slide mechanisms, inserts, and cooling channels can be integrated into the mould design to enhance functionality and reduce production cycles.
The efficiency of dashboard moulds directly impacts manufacturing productivity. A well-designed mould can facilitate faster cycle times, minimize waste, and ensure consistent quality across production runs. This is particularly important in industries like automotive manufacturing, where high volumes of parts are required, and any delay can lead to significant financial losses.
Moreover, the trend towards customization in automotive interiors has led to an increased demand for dashboard moulds that can accommodate various designs and features. Manufacturers are now leveraging advanced technologies, such as computer-aided design (CAD) and computer-aided manufacturing (CAM), to create more complex and detailed molds that meet the evolving needs of customers.
In summary, dashboard moulds play a pivotal role in the plastic injection molding process, significantly influencing both the quality and efficiency of production. By understanding the intricacies of these molds, manufacturers can optimize their operations, reduce costs, and enhance product offerings. As the industry continues to evolve, staying informed about advancements in mould technology and design will be key to maintaining a competitive edge in the market.