There are different engineering plastic polymers suitable for medical injection molding. These plastics – are mainly thermoplastics and not thermosets because of their superior performance over the latter.
- Polyetheretherketone (PEEK)
PEEK is a common engineering-grade thermoplastic with outstanding resistance to harsh environments, including against radiation, high temperature, chemicals, wear and tear conditions, etc. It is mainly for creating medical and surgical implants.
Moreover, it guarantees impeccable dimensional stability, even after exposure to stress. It also possesses other top-notch mechanical properties, making it an excellent fit for manufacturing medical gadgets. In addition, it is compatible with injection molding and other manufacturing techniques used in fabricating medical equipment.
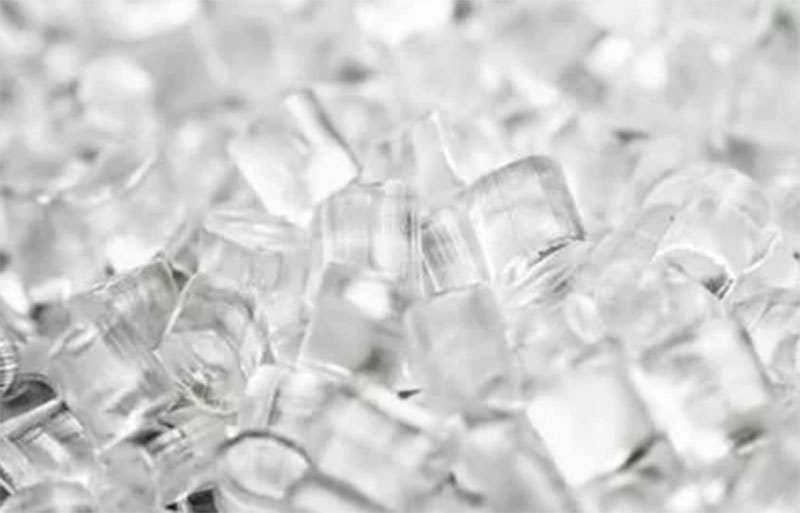
- Polyethylene (PE)
Polyethylene is a common medical-grade plastic polymer. It comprises thousands of ethylene polymers, with the resulting material possessing high tensile strength and rigidity.
PE’s compatibility with biological tissues and resistance to harsh environmental conditions, including sterilization makes it a valuable plastic for medical injection molding. It is suitable for manufacturing joint prostheses, connectors, tubings, pharmaceutical containers, etc.
- Polycarbonate (PC)
Polycarbonate is a strengthened engineering thermoplastic formed from bisphenol A and phosgene condensation. Though it appears transparent, it possesses excellent mechanical properties, including toughness, flexibility, resistance to abrasion, breakage, temperature, etc.
Also, it is highly compatible with body tissues, a typical characteristic of medical-grade plastics. It is suitable for manufacturing many medical plastic injection parts, such as transparent masks, protective gear, oxygenators, etc.
- Polypropylene (PP)
Polypropylene is another common plastic polymer for plastic injection molding, resulting from the condensation of several propylene units. It possesses incredible toughness with resistance to cracking, radiation, impact, temperature, wear, and tear, etc.
All these make it a suitable plastic for manufacturing components for the health sector. It is ideal for manufacturing connectors, tubings, syringes, knee and hip replacements, respirators, etc.
- Silicone
Silicone is a chemically inert chemical compound resembling synthetic rubber with outstanding mechanical properties and compatibility with biological tissues. It is the go-to medical-grade plastic polymer when flexibility is a priority.
It is suitable for manufacturing products and devices like catheters, cosmetics products, contact lenses, breast implants, drug delivery systems, connectors, and tubings, etc. In addition, silicone is exceptionally cost-efficient for manufacturing medical gadgets.
- Polystyrene (PS)
Polystyrene is another top-notch engineering-grade plastic suitable for manufacturing medical injection molding parts. Unlike most other thermoplastics discussed earlier, it has little to no flexibility yet offers other excellent mechanical attributes and compatibility with body tissues.
It is resistant to harsh conditions that help ensure high dimensional stability, which is vital for all medical components. It is common for manufacturing Petri dishes, culture trays, and other diagnostic parts.