- Mold Design and Creation
The mold is the most significant part of injection molding. When planning to engage in injection molding, the first thing to do is to create the injection mold component, which determines the shape, size, and structure of the intended fabrication.
Machinists often utilize CNC machining (or 3D printing) to manufacture the mold to the desired specification to ensure accurate geometry, dimensions, and draft angles, among other features. A typical injection mold is made from aluminum or steel and features mainly the core and cavities, including components like gates, runners, spruces, and ejector systems.
- Material Selection
After creating the right mold type for the intended fabrication, the next step is selecting the plastic polymer that best fits your project. You should consider strength, flexibility, chemical resistance, and temperature tolerance, which determine the suitability of the material for the intended application. Standard plastics for injection molding include ABS, polypropylene, and nylon, each offering unique mechanical and chemical properties. - Machine Setup
Setting up the injection molding device involves configuring parameters such as temperature, pressure, and cycle time. In addition, the operator must ensure mold alignment, the loading of raw plastic materials, and the testing of the injection system before production begins. - Injection Molding Cycle
As mentioned earlier, the injection molding cycle starts by melting the plastic and injecting it into the mold at high pressure. As molten plastic fills the cavity, it begins to take the shape of the mold, forming the part as it cools and solidifies.
In addition, the cooling time for injection molding depends on the selected material’s properties, thickness, and size of the molded part. Cooling channels within the mold cavity may accelerate the process, ensuring the part retains the intended shape and reducing the risk of warping or other injection molding defects.
- Parts Ejection
Once the molten plastic has solidified, the mold opens, and the finished part is ejected using ejector pins or plates. This step is automated to prevent opening before cooling, speeding up the production process and avoiding damage to the part. - Inspection and Post-processing
After the part is ejected, the manufacturer will conduct quality checks to ensure it meets dimensional accuracy and surface finish standards. Inspection methods include visual checks, dimensional measurements, and testing for structural integrity to maintain product consistency.
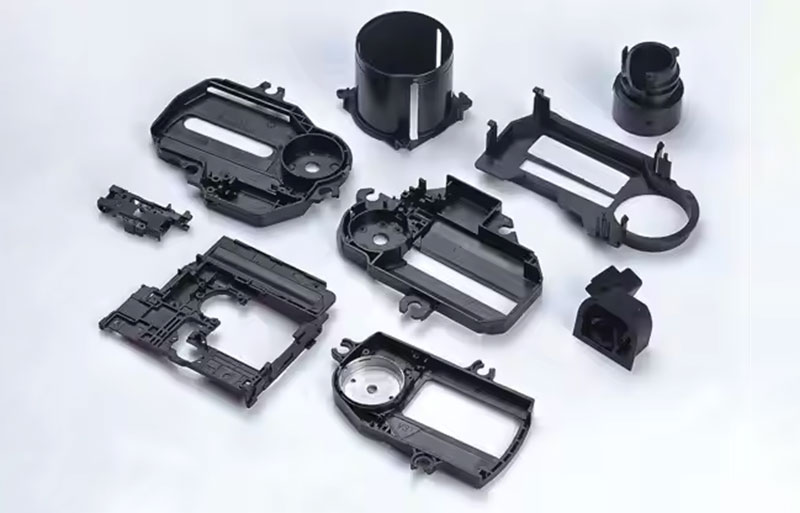
Afterward, depending on the intended specification, the manufacturer may proceed to post-processing finishes that suit the injection-molded part.