Injection molding includes techniques that involve creating components by turning plastics into liquid before reshaping. Below, we examine the common injection molding types.
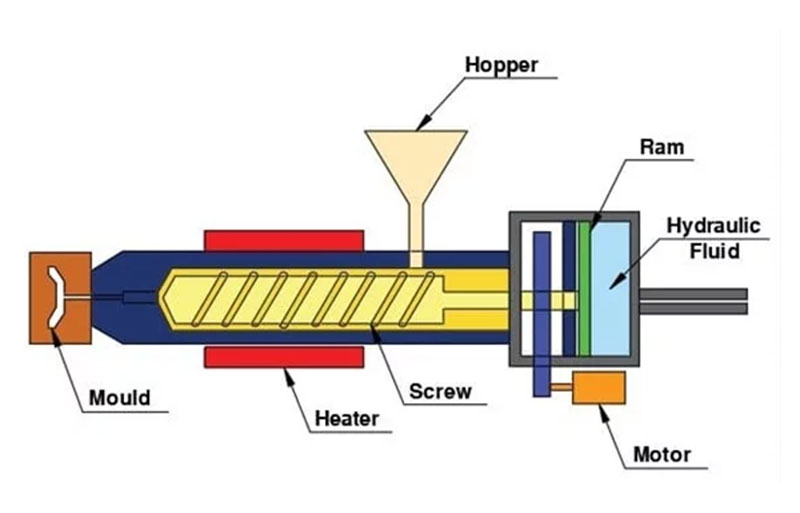
Insert Molding
The insert molding method involves placing a pre-made component, such as a metal insert, into the mold before injecting the liquefied plastic resin. In this way, the insert component integrates with the plastic, forming a rigid component of multiple materials. The process is the go-to choice for creating plastic parts that require metal threads.
Blow Molding
Blow molding is the go-to process for creating hollow plastics, such as bottles and containers. The process involves heating the plastic and using air pressure to force it against the walls of the mold, creating a hole. Like in all injection molding processes, the resulting fabrication takes the shape of the mold cavity, creating lightweight and durable containers used in the packaging industry.
Overmolding
Overmolding involves molding one material over another, creating a combined structure. Like insert molding, the resulting part usually comprises two different materials: hard plastic and softer polymer. This process is commonly used to improve grip, where manufacturers add an elastomer, such as rubber, to tool handles.
Liquid Injection Molding
Liquid injection molding, also known as liquid silicone rubber, is a process that uses thermoset polymers to create flexible and heat-resistant parts. The molten material is heated and forced into a mold, curing quickly and forming the desired structure. The process is more common when creating seals and gaskets in the medical industry.