There are different thermoplastics for fabricating hospital and medical injection parts. However, each polymer suit better for specific applications. Let’s discuss the criteria to consider when selecting medical-grade plastics.
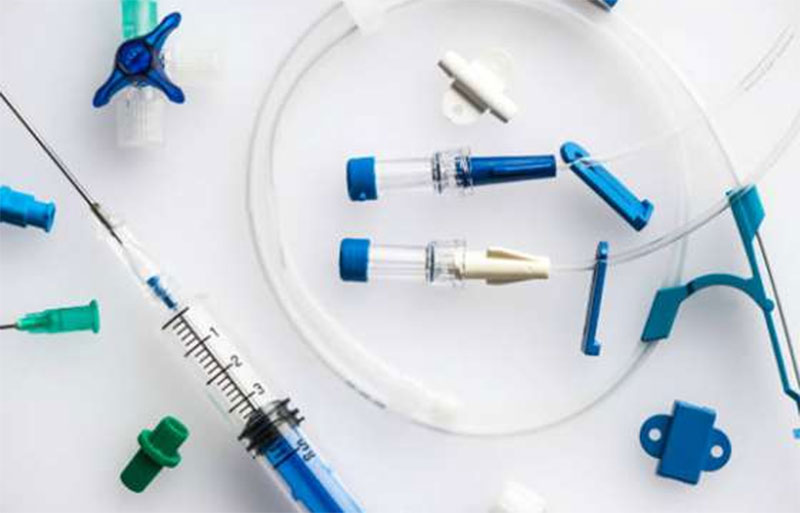
1. Industry (FDA) Regulations
When designing components for medical equipment, the first thing to consider is its compliance with the appropriate authority, mainly the FDA. There are guidelines and requirements that every medical instrument must meet before its eligible for use by the general public.
These standards include compatibility with biological tissues and the ability to withstand extreme physical and chemical conditions. Other criteria are subject to these regulations. Therefore, if the plastics pass all FDA regulations, they are suitable for fabricating medical plastic injection parts.
2. Strength and Durability
Plastics for manufacturing medical injection parts must show marked mechanical properties relating to strength, rigidity, and durability. When designing components for the health sector, it is crucial that you avoid fragile plastics that can break easily. Instead, use those impact and shatter-resistant thermoplastics, which will serve their purpose of creation for extended periods.
3. Suitability of the Environment Within the Organism
Some medical products, such as prosthetics and surgical implants, will directly contact organic tissues. Therefore, plastic polymers for such fabrications must be inert and not alter normal body activities. Instead, remain compatible with the environment of the internal body structures even after use for a long time.
4. Ability to Withstand Sterilization Conditions
Many medical devices need to be sterile – free of any contaminants and microorganisms which may be harmful to patients. That said, the sterilization process involves exposing these medical gadgets to harsh conditions, such as; high temperatures, radiation, or chemicals.
Therefore, the plastic polymers for creating instruments that require sterilization must retain their dimensional accuracy even after exposure to these harsh environments.
5. Selection of Molding Method
The injection molding method is another criterion for consideration when selecting the right medical plastics. For example, it is best to use liquid silicone injection molding for such fabrication when working with silicone.
Other plastic injection molding techniques include insert molding, micro molding, ultrasonic bonding, overmolding, etc. It should ensure to use of the appropriate process for your fabrication.
6. Consider General Usage
The purpose of the fabricated components is another thing to consider when using plastic polymers for medical injection molding. For example, medical equipment like gloves, masks, respirators, tubings, catheters, and syringes are for single use.
As a result, such components should utilize only a few materials during fabrication; they should be flexible, lightweight, transparent, and easy to sterilize. Spending too much on such products will be too expensive and unwise for the manufacturer.