An injection molding gate design directly affects the outcome of a plastic mold. A well-designed gate manages the volume and direction of the molten plastic that flows into the mold. This is because you wouldn’t want molten plastic flowing toward the runner/nozzle instead of the mold.
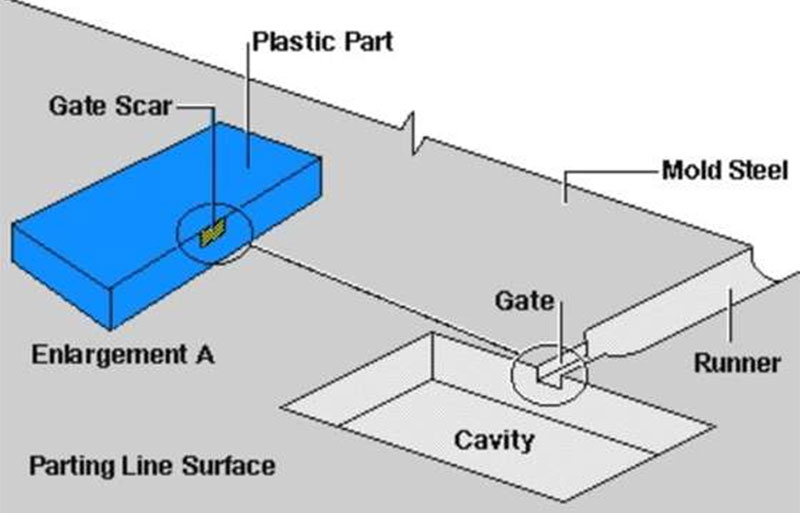
In addition, the mold gate design ensures that the molten plastic reaches every area of the mold before cooling occurs. Thus, it prevents the uneven and untimely hardening of the molten plastic. Also, it ensures that plastic parts do not sustain deformations such as breaks or stress fractures.
What’s more, the injection molding gate produces heat through dissipation. An ideal gate design increases polymer temperature to stop the formation of flow marks and weld lines. With the injection molding process simplified, manufacturers and product designers can eliminate runners to make post-processing treatment easier.